Posted on Aug 27, 2021
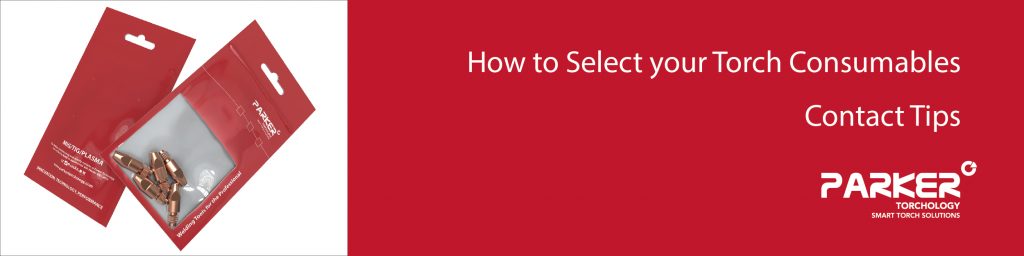
In this blog series, we discuss how to improve productivity and weld quality by selecting the correct contact tip for your job. It can be tempting to try to use the same consumables for every welding job to make set-up easier, however this isn’t always the best idea.
The overall aim of selecting the correct contact tip is to optimize the transfer of the welding current to the wire as it passes through the tip, while ensuring that the wire feeds through the tip with minimal resistance.
What Material?
Copper is the industry standard material for contact tips for a reason – it has incredibly good conductivity. However, the downside of copper is that it is a relatively soft material and over time the wire can wear the inside of the tip. To improve the lifespan of our contact tips, Parker Torchology manufactures using high-quality copper alloys. This offers high conductivity, combined with longevity and reliability.
We also offer Copper-Chrome-Zirconium (CuCrZr) contact tips which have marginally less conductivity than Copper, but are more hardwearing and will withstand higher temperature. So they are worth considering for jobs where high amperage is necessary, and/or where there will be a long arc-on time.
What Size?
Generally, it is recommended to use a contact tip with the same size bore as the as the wire diameter. An undersized tip can increase friction, which affects wire feeding. However, an oversized tip bore can affect current transfer, which will increase operational heat.
For soft wires such as Aluminium, an oversized contact tip allows the wire to feed with little pressure, reducing the risk of the wire bunching up or kinking.
Why Does Quality Matter?
Contact tips play a vital role in the Mig welding process. Although they may be seen as a minor component, they have a significant impact on productivity and weld quality. Our contact tips are machined to high tolerances, ensuring the best thermal and electrical conductivity. This minimizes heat build-up and electrical resistance, maintaining a consistent conductivity and reducing arc problems. This precision machining also allows the wire to feed smoothly through the tip with low friction and resistance, reducing issues such as burnback.
All Parker Torchology wear parts are manufactured to the same specification as the original manufacturer ensuring reliability, longevity and superior performance. For more advice on selecting the right Mig welding contact tip, contact our knowledgeable sales team today.